Petromidia Refinery
The pillar of the refining industry
The largest Romanian refinery and one of the most modern refineries in South East Europe, with a material impact in Dobrogea region and at national level.
Petromidia makes a significant contribution to development of Rompetrol’s business in Romania and in the Black Sea region. It plugs in the trading and supply business lines with fuel distribution in Rompetrol’s stations in Romania, Republic of Moldova, Bulgaria and Georgia.
Strategic positioning at the Black Sea
Petromidia enjoys a strategic position on the shores of the Black Sea, in Navodari, 20 km north of Port of Constanta.
Logistic benefits:
- own marine terminal
- facilities in Port of Midia: berths nos. 1-4 for crude oil and products, and berth no. 9 (A, B and C) for export of oil products.
- own logistic railway system
- access to Danube-Black Sea Canal
The marine terminal is the most important logistic asset of the refinery; it is located 8.6 km at sea, and can received ships of up to 160,000 TDW. With this terminal and the entire logistic system developed by the company in the region, Romania can become a regional energy hub, a connecting platform between the natural resources of Asia and the European demand for feedstock processing and production of oil products.
A complex refinery
Petromidia has a Nelson complexity index of 11.4, and processes crude oil with high sulphur content, obtaining only Euro-5 oil products.
Aligned to the BAT (Best Available Technologies) standards, Petromidia is also the first Romanian refinery to have successfully aligned to the European environmental regulations and fuel quality standards.
In order to achieve the current refinery complexity and ensure full compliance with the environmental requirements of the European Union, the Group invested over USD 450 million.
The refinery has the highest yield of white products in the region (85%), and ranks 9th among the 250 refineries in Europe and Africa*.
*Wood MacKenzie 2015
Production units of the refinery
- atmospheric and vacuum distillation units
- full range of hydrotreatment units
This complex set allows the refinery to obtain high yields for its white products.
- one for gasoline
- one for kerosene
- two for diesel
- three conversion units:
- mild hydrocracking
- fluid catalytic cracking
- delayed coker
- new support units, such the sulphur recovery and tail gas treatment unit
- hydrogen, nitrogen and flares plant
- two modern line mixers for gasoline and diesel
Decrease emissions of sulphur dioxide
Petromidia refinery has a new modern liquefied petroleum gas recovery unit, a system that ensures a substantial reduction of sulphur dioxide emissions from the gases discharged to the refinery chimneys - significantly below the limit imposed by the European Environment regulations.
With a value of 4.6 million USD, this is a unique project in Romania and it is part of the Group's strategy of continuous modernization of the operational processes at the level of the two production units - the Petromidia Navodari and Vega Ploiesti refineries.
Find out more about LPG recovery by reading our press release here.
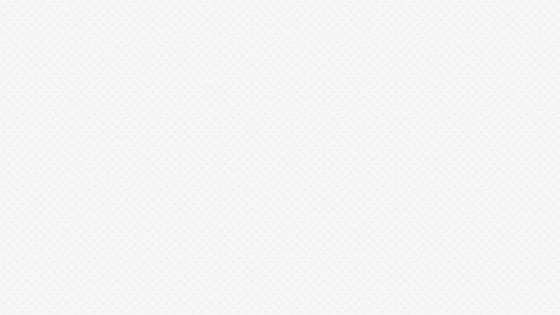
Digital transformation
Rompetrol Rafinare will invest 4 million USD for implementing a digital solution aiming at identifying optimal conditions for increasing the capacity, product quality improvement and reducing energy consumption in Petromidia refinery, Navodari.
All these aspects lead to the fourth industrial revolution – Industry 4.0, and Rompetrol continues to be a local pioneer by launching a comprehensive digital transformation program at the Petromidia refinery in Navodari.
The implementation of the digital solution - Advanced Process Control (APC) began in 2017 as a pilot project at the Atmospheric and Vacuum Distillation Unit (DAV) – one of the most important units in the processing of crude oil that ensures the raw material for the rest of the installations from the refinery.
Find out more about APC by visiting our press release, here.
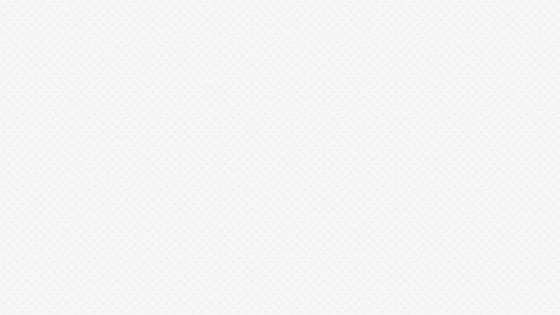
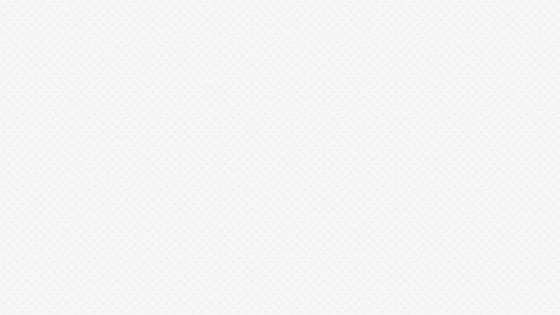
Automation of “In line Blending” Unit
The total investment of 3 million USD represents a new stage of the digital transformation program of the Petromidia refinery.
The implementation of the new digital system ensures detailed real-time analysis of the components and the final product obtained and, implicitly, a careful monitoring of fuel quality and compliance of them with the legislation in force.
The quality of the product obtained after the blending process is monitored and controlled through on-line analyzers, which transmit the data in real time to the operators.
More details here.
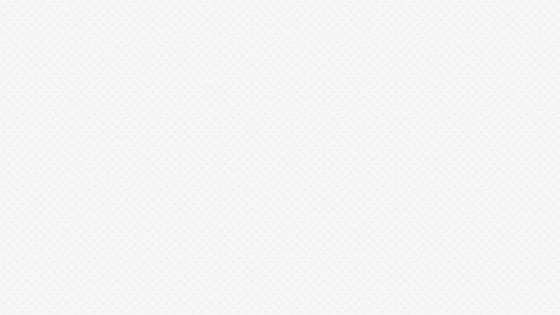
Petromidia Refinery, 40 years of operation
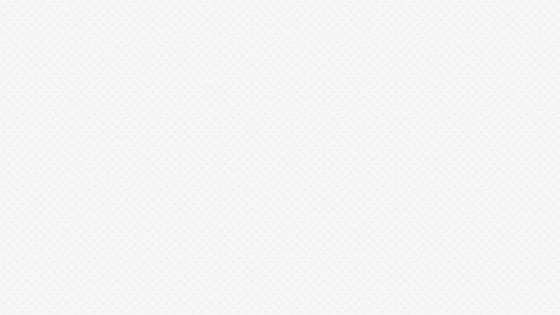
Investments
2008 – 2012 - a new beginning
The most important engineering project was the program for modernization and refining capacity increase up to 5 million tons per year, amounting to more than USD 450 million.
Key objectives of modernization program:
- Increasing the operational capacity of the refinery up to 5 million tons/year.
- Meeting the EU and Romanian fuel quality standards - Euro-5 (regulation COM (2005) 693)
- Increasing diesel production with 8% (from 37% up to 45%)
- Rendering operation of the refinery compliant with the EU and Romanian environmental regulations (BAT system) (Directive 70/220/EEC)
- Increasing mechanical availability and reliability for the refinery.
The new setup of the refinery includes:
- Modernization of the Fluid Catalytic Cracking (FCC) plant (to process inflows from the Mild Cracking plant).
- Modernization of the existing Claus plant (to reduce NOx emissions).
- Modernization of the VGO hydro-treating to diesel plant (to process the increased future quantity of diesel).
- Modernization of the amine plant (to process additional gas with hydrogen sulphide).
- New Units
- Mild Hydrocracking plant (the key unit of the modernization package).
- The new hydrogen plant (to supply hydrogen to the retrofitted MHC and VGO HDT units).
- A new sulphur recovery plant (to process the future sulphur capacity).
- A new flares system (to support the new units and the existing refineries).
- Increasing the N2 liquid evaporation and automation capacity (to supply nitrogen to the retrofitted refinery).
150 million USD strategic investments in Petromidia
In 2024, Rompetrol Rafinare allocated a total investment budget of almost 150 million USD, of which 85 million USD were invested in modernization and development projects for operational assets during the general turnaround of the Petromidia refinery.
Hydrogen Power Plant (HPP) Modernization
Rompetrol Rafinare, the company that owns and operates the Petromidia refinery, has refurbished the high-purity hydrogen (HPP) plant following an investment of almost 10 million dollars. The most important and complex part consisted of changing the 114 vertical tubes that store the catalyst necessary for the reforming reaction and obtaining hydrogen. The plant has a capacity of 40,000 cubic meters/hour, with a purity of at least 99.99%.
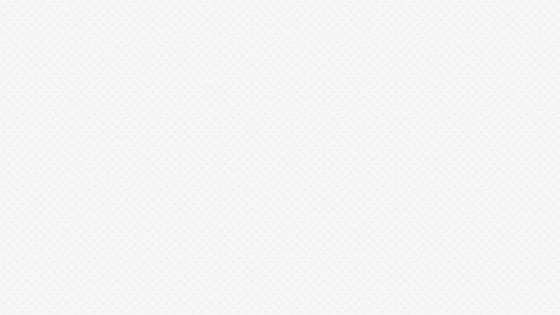
Modernization of the Delayed Coking Unit
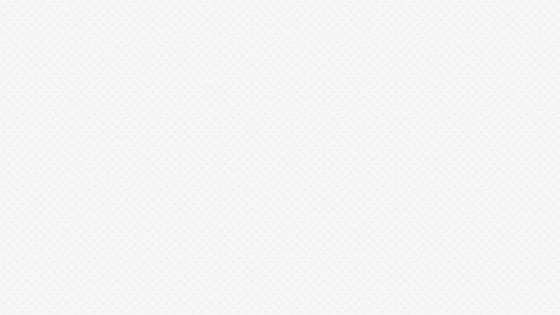
One of the primary units at the Petromidia refinery is the Delayed Coking Unit, which plays a crucial role in maximizing the value of crude oil and producing high-value-added semi-finished products essential for the Rompetrol refineries, Petromidia Navodari, and Vega Ploiesti. The recent USD 13 million investment was completed during the Petromidia refinery's turnaround and involved implementing an advanced technological system that optimizes energy consumption and enables remote automated operation. This investment helps reduce environmental impact while also enhancing employee protection and safety.
State-of-the-art reactors installed at the Petromidia refinery
One of the most important projects implemented during the general turnaround of the Petromidia refinery was the investment in two modern reactors, part of the Middle Distillate Hydrotreating (HDV) unit. The role of this unit is to process diesel mixtures resulting from the technological processes of other facilities in the operational flow, aiming to eliminate sulfur compounds and, implicitly, to obtain EURO 5 components for the final production of diesel.
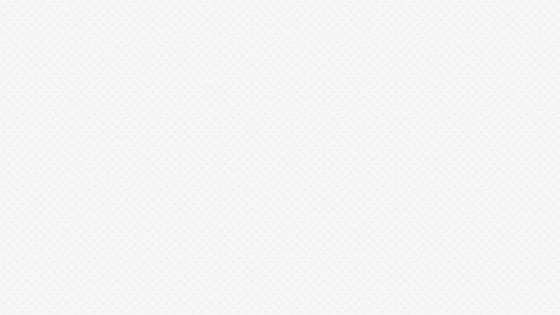
Modernization of the CO Boiler in the Catalytic Cracking Unit
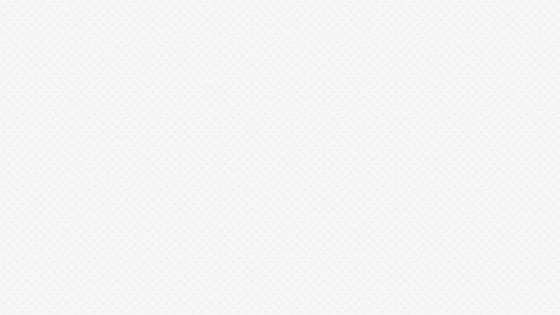
With an investment of approximately four million dollars, the company completed a project to convert the CO Boiler of the catalytic cracking unit (FCC) from natural water circulation to forced multiple circulation. The major transformation consisted in installing a boiler water recirculation system, which makes it possible to operate at a minimum capacity of 35 tons per hour (compared to the original minimum capacity of 50 tons per hour), flow rate which can increase up to a maximum of 90 tons per hour, depending on the needs of the refinery.
Figures that matter
Results 2024
The general turnaround of the Petromidia refinery represented a major financial and operational effort, aimed at maintaining an optimal level of operation of the refinery, in the best conditions of safety and labor security.
Although the refinery's activity was halted for 2 months for the turnaround works from March to May, 4.62 million tons of raw materials were processed in the Petromidia refinery.
Petromidia recorded a white product yield up by 2.81% compared to the previous year – 86.88%wt, and Jet fuel yield reached a record 8.7%, with a production of about 400 thousand tons in 2024, a level close to the record of 2019.
Also, in December 2024, the Petromidia refinery achieved a record level of daily crude oil processing for the winter period with an average of 15 thousand tons per day (crude oil only).
Read more about the financial and operational results in 2024
2021 | 2022 | 2023 | 2024 | |
---|---|---|---|---|
![]() |
16,300tons /day |
15,409tons /day |
14,000tons /day |
15,360tons /day |
![]() |
4,58million tons /year |
5,26million tons /year |
5,01million tons /year |
4,62million tons /year |
![]() |
86.12
|
85.55
|
84.1
|
86.88
|
![]() |
102.78
|
96.2
|
101.3
|
97.49
|
![]() |
95.96
|
87
|
92.44
|
89.75
|
![]() |
0.82
|
0.80
|
0.66
|
0.77
|
![]() |
9.81
|
9.57
|
9.57
|
9.54
|
Key figures- modernization and capacity increase program
Indicators | 2008 | 2012 |
---|---|---|
Capacity in mil. tons/year | 3.5 | 5 |
Nelson index* | 8.3 | 10.5 |
Kerosene and diesel %wt | 2.6/38 | 5.5/45 |
Diesel in mil. tons/year | 1.5 | 2.5 |
Gasoline in mil. tons/year | 1.3 | 1.4 |
Kerosene in mil. tons/year | 0.15 | 0.3 |
Modernization program in figures
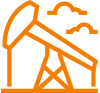
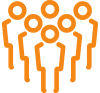
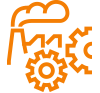
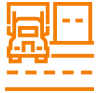
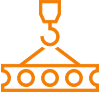
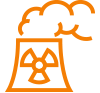